°OMG I’m so relived today. Remember a couple of day ago in my last Reader’s Questions post where I confessed that I’d recently had two failed double batches of Clarity? The ones that looked like this when cut?
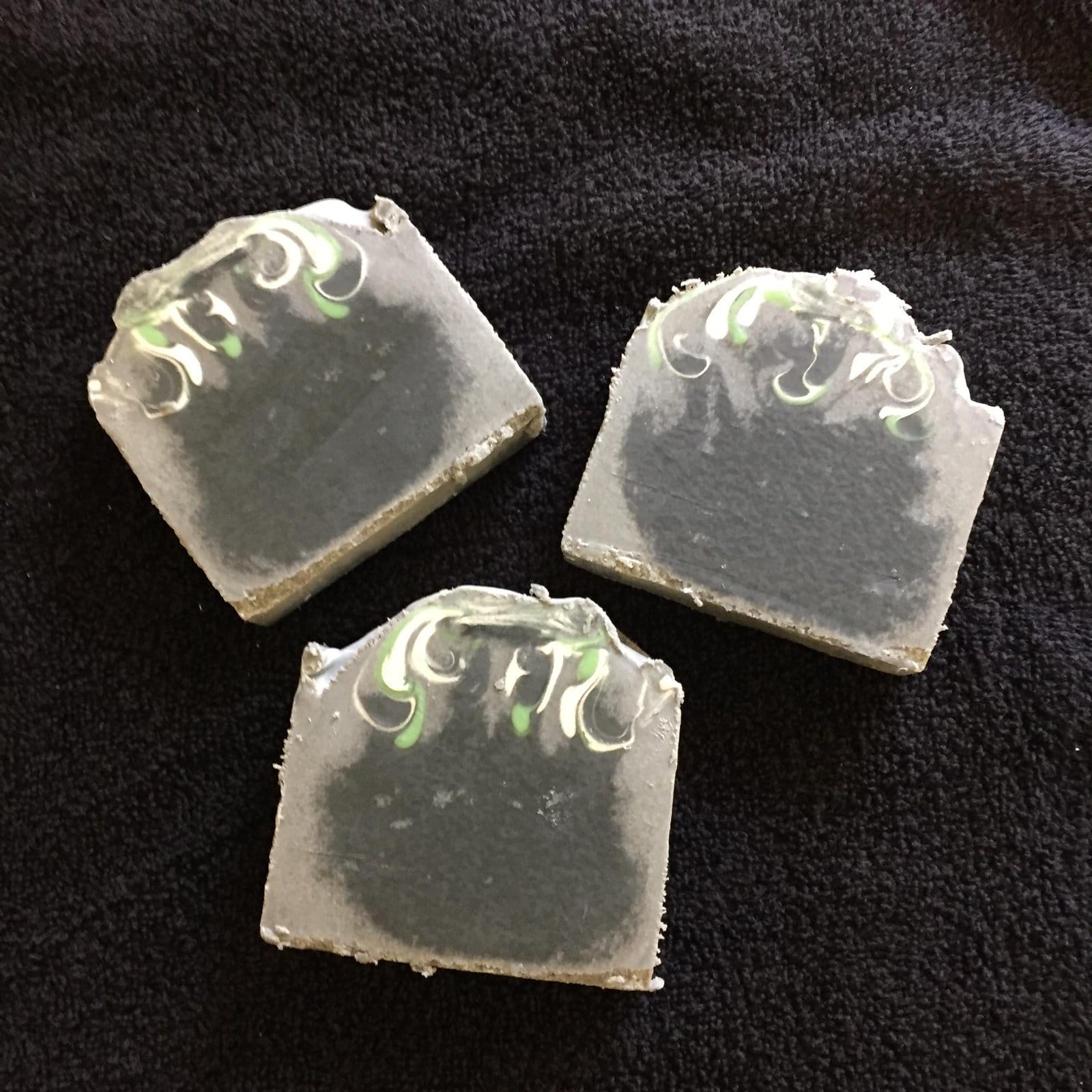
6kg / 12lbs of soap that I don’t know what to do with (except I might have a plan, which I’ll come to in a moment..)
Anyway, it was with much trepidation that I decided I had to attempt making it again. It’s a REALLY good seller, and I can’t afford to run out, but I was nervous – wasting more precious oils (both regular and essential!) wasn’t an option. I had decided that it was probably down to a partial gel situation, and it would appear that, contrary to what I said here about changes in the weather not affecting my soapmaking, recent changes in the weather had indeed affected my soapmaking (Gah! This is where making bold statements in a blog post gets me!!!!)
I decided to try the CPOP (Cold Process Oven Process) method. I made the soap with the oils and lye solution just a little warmer than room temp (I usually soap at room temp) and preheated both ovens (on the dough proving setting) to just 40°C. I had to use both ovens as I make two loaves at a time but can only fit one in at time:
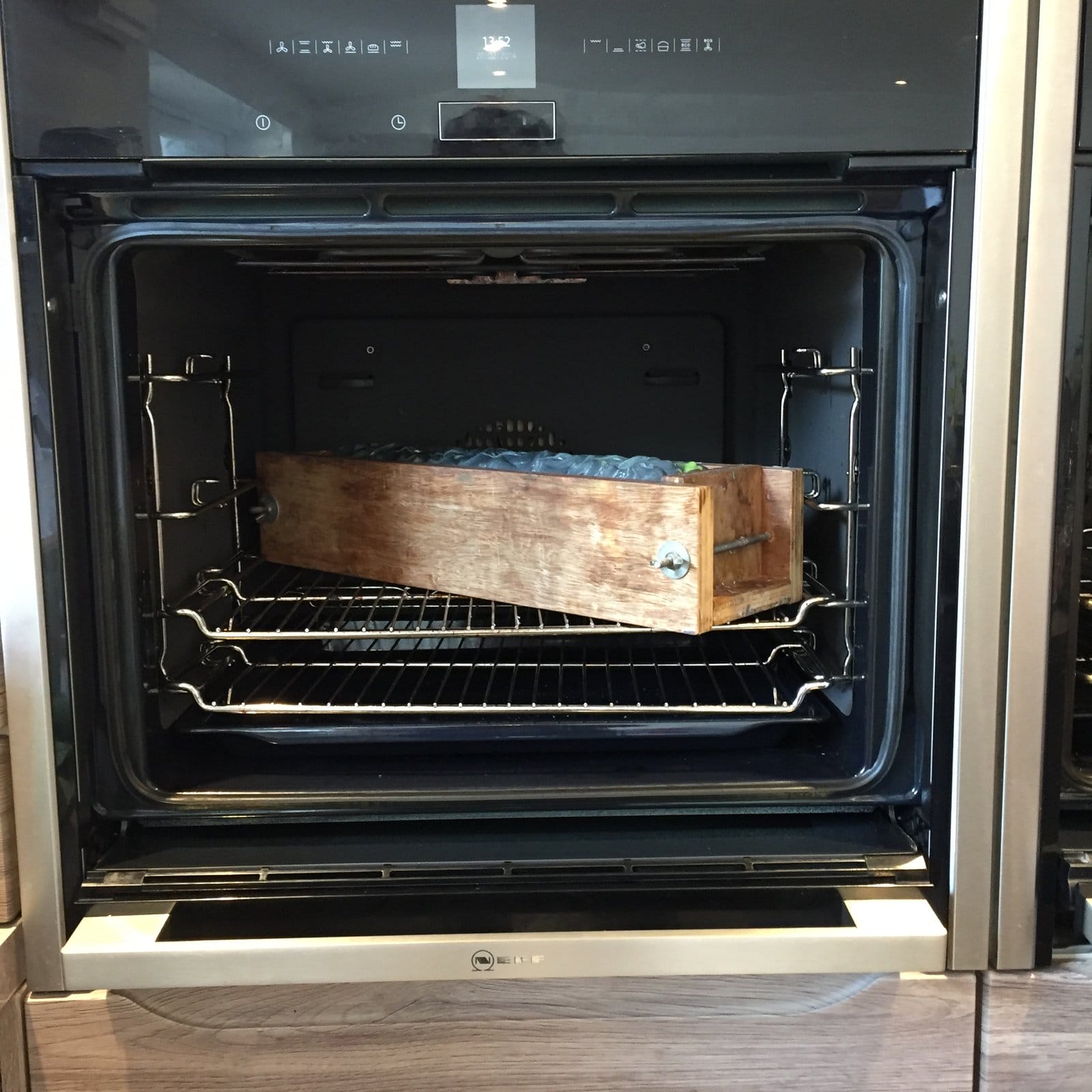
I did actually try to take a pic with the door closed but it didn’t quite come out as planned :-D:
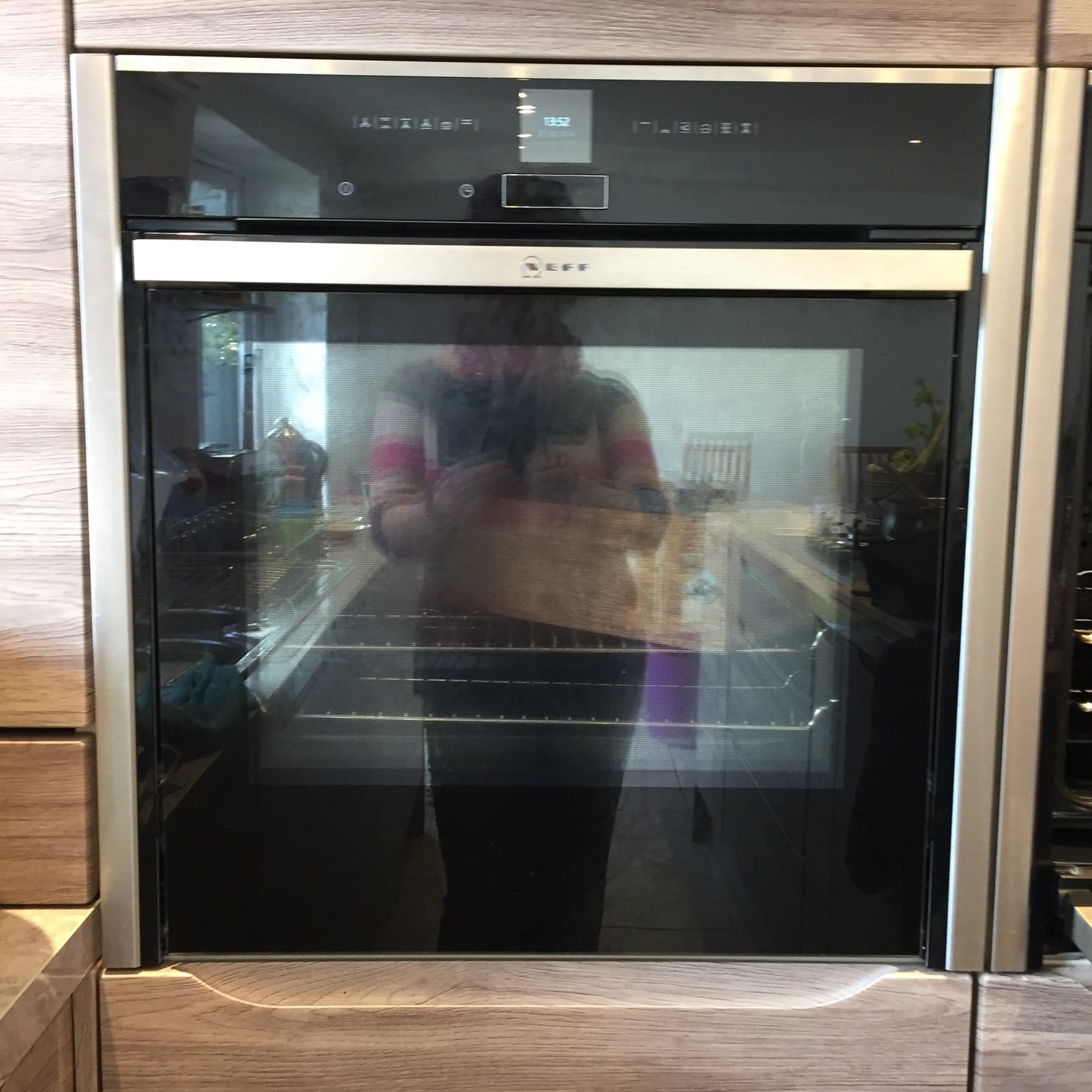
So, I left the moulds in there for an hour, then turned off the heat and left them there for another hour.
When I took them out the tops definitely looked different to my non-CPOPped batches:
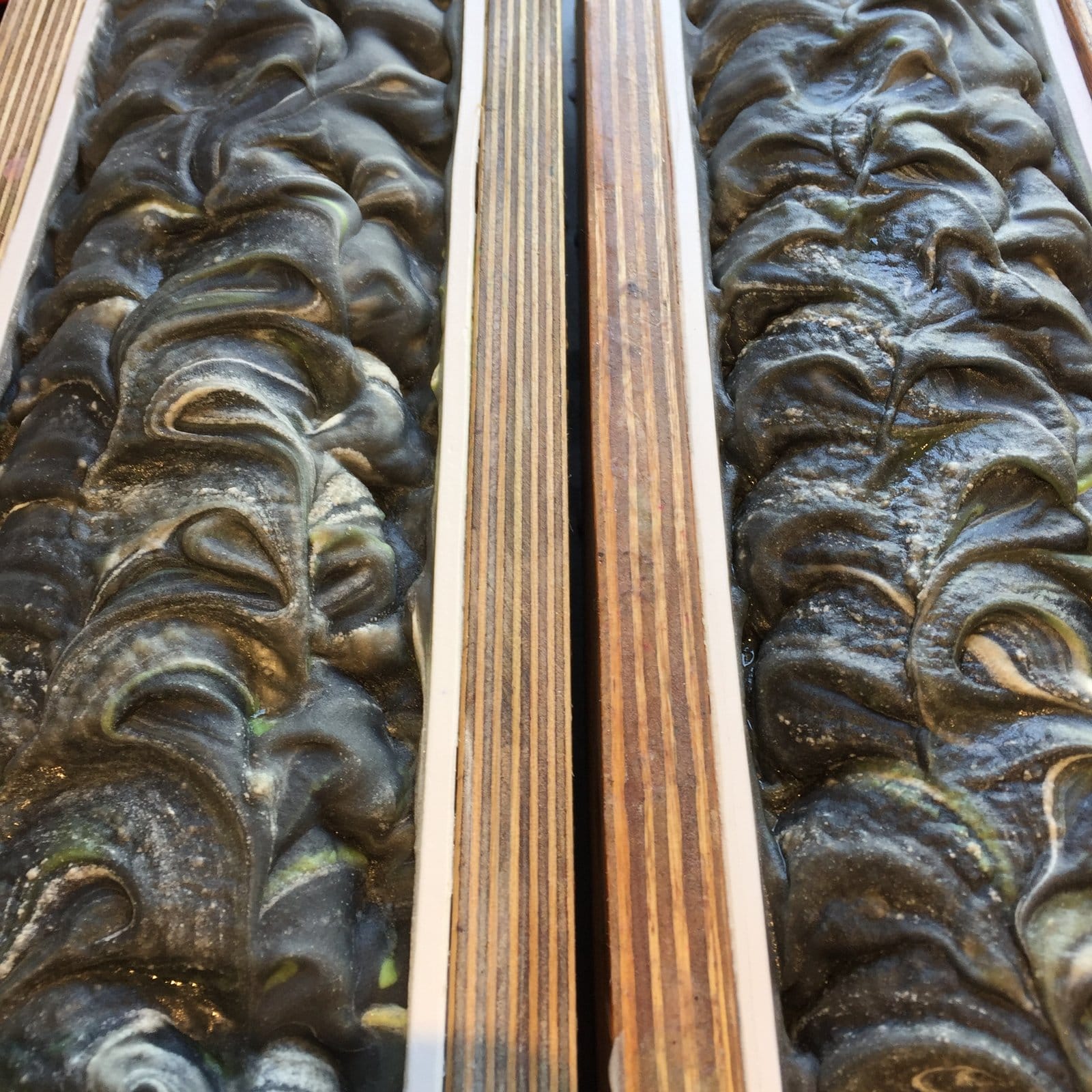
And then, a mere 24 hours later (I usually leave them in the mould for 48 hours) I cut the first one loaf, practically holding my breath as I brought the wire down for the first slice…Success!! (but do bear in mind that these are freshly cut and not yet tarted up…)
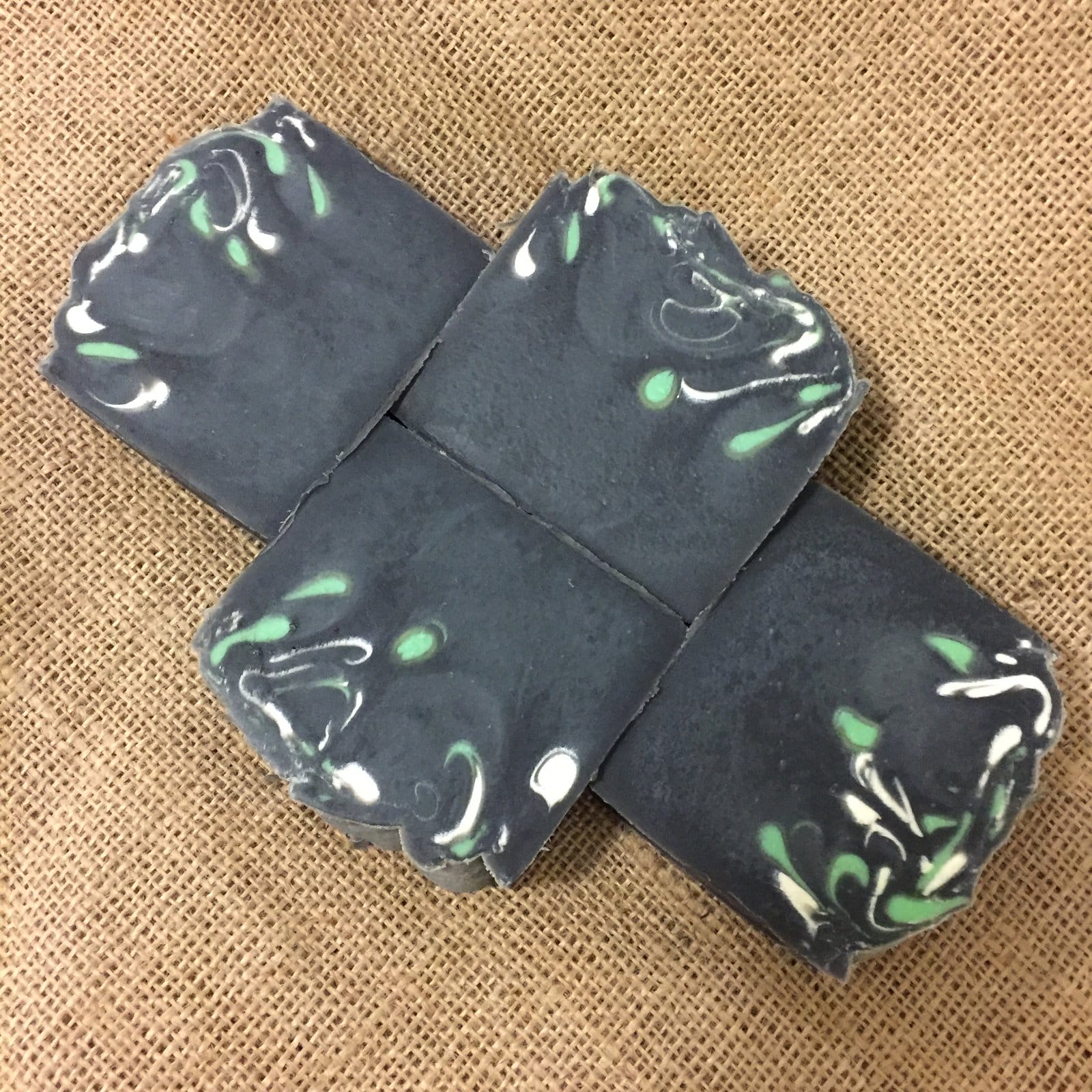
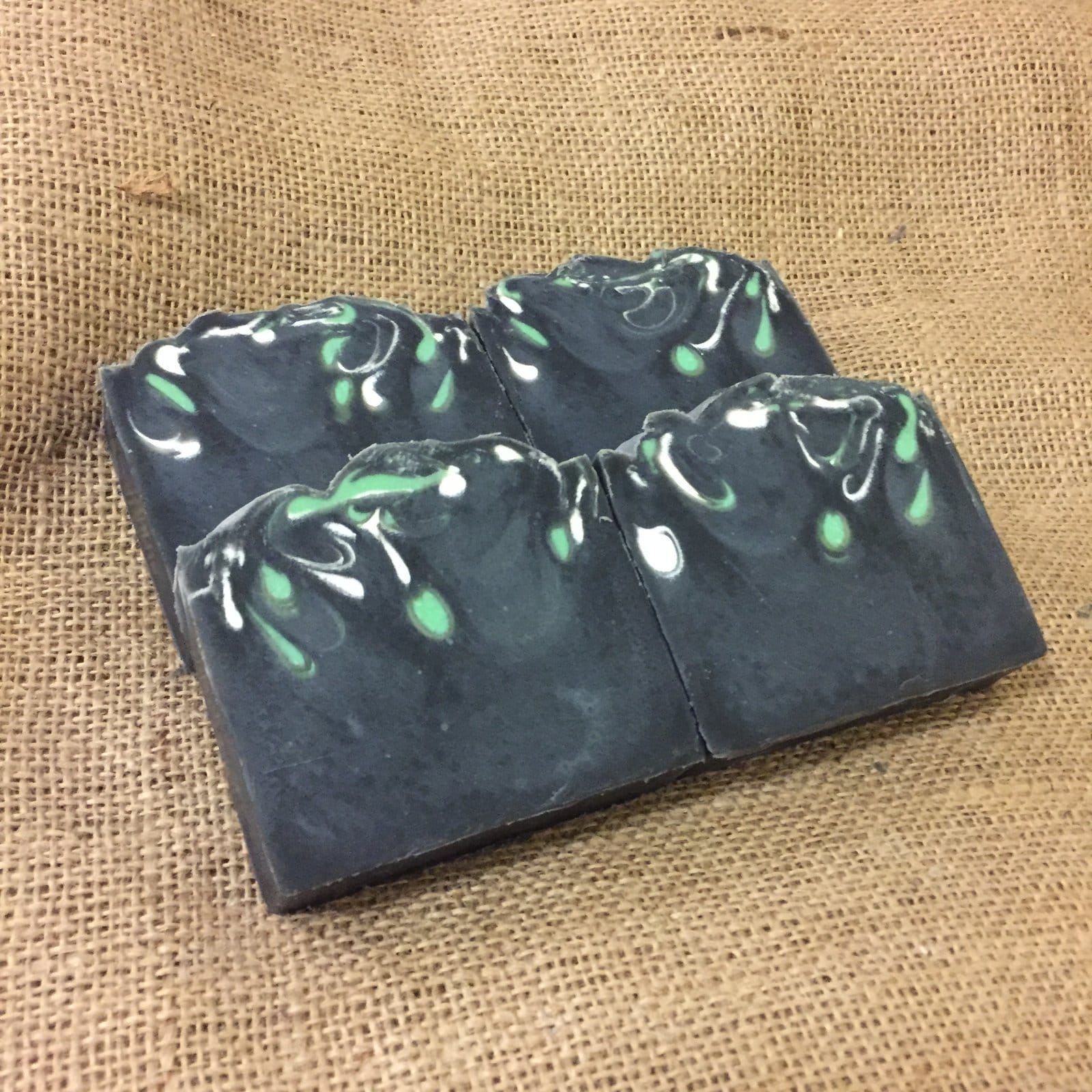
Cue a little happy dance…
And what to do with the other 6kg of spoiled soap? Well, in the comments section of this post where I also shared my ‘fail’, Sly of Soaps by Sly was kind enough to share a video of Tania of Soapish showing a method that seems to ‘fix’ a partial gel. This could be a gamechanger, and I’m definitely planning on giving it a go (just don’t ask me when!!)
Thanks for reading – back tomorrow!
Vickx